Elkem Solar - Raw Material System
Central Conveyors was appointed to engineer a sophisticated conveying system for transporting a precise mixture of silicone and calcium to a furnace at exceptionally high temperatures. The final product serves as a component in solar panel manufacturing.
​
Our Solution
The project scope encompassed the precise delivery of both materials in specific proportions to the furnace for processing. Our engineering team designed and fabricated four stainless steel silos, with two designated for calcium storage and two for silicon. These silos were positioned above belt conveyors equipped with precision weighing scales. The automated system utilises valves that regulate material discharge based on predetermined weight parameters. Once the target weight is achieved, the scales transmit a 24-volt signal to the silo valves, initiating closure. The conveyor system then activates, commencing material transport to the furnace.
​
The materials progress from the scaled flat belt conveyor to a bucket elevator, achieving a vertical elevation of 10 metres. These specialised vertical conveyors feature belt-mounted buckets that transfer the materials onto troughed vibratory conveyors. The vibratory mechanism facilitates material movement through oscillation. Traditional belt conveyors were deemed unsuitable due to the extreme temperatures at the furnace interface.
Central Conveyors also engineered the comprehensive control system, incorporating Siemens hardware and PLCs. Our expertise extended from initial dispensing to final delivery. Central Controls Ltd, a division of the Central group, managed the entire system's design, manufacture, and programming, enabling us to deliver a complete turnkey solution.

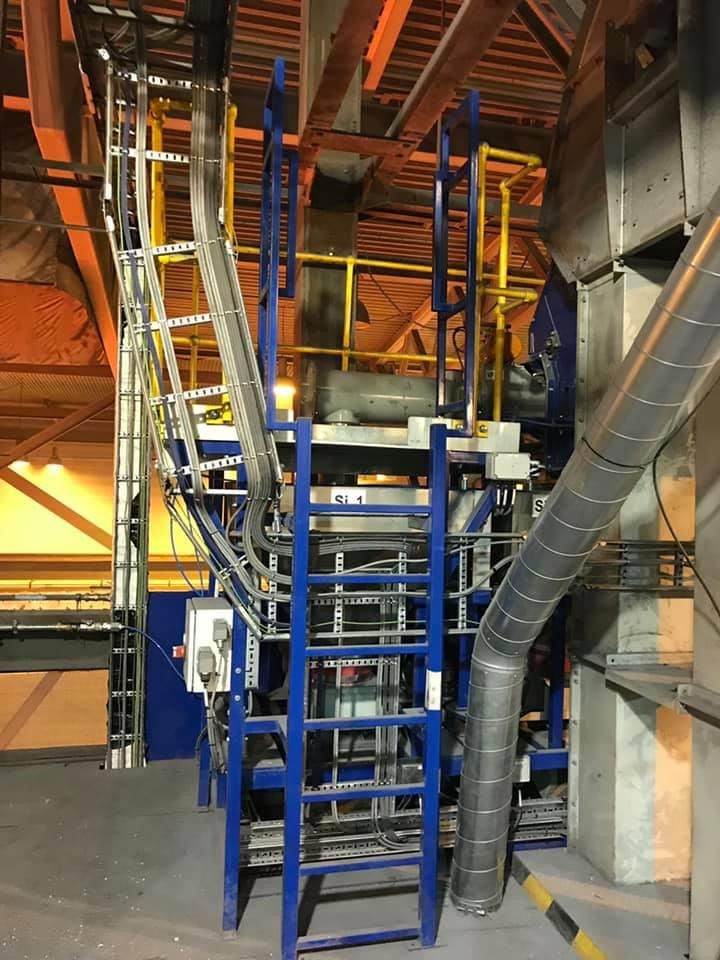

